Nylon conveyor belt
Nylon conveyor belt is widely used in mining, coal yard, chemical industry, metallurgy, construction, port and other departments. Nylon conveyor belt is suitable for conveying non-corrosive bulk, granular, powder materials, such as coal, coke, sand, cement and other bulk materials (materials) or component articles, conveying various bulk, granular, powder and other loose materials with accumulation density of 6.5~2.5t/m3, can also be used for the transportation of adult articles. Compared with ordinary cotton cloth core conveyor belt, nylon conveyor belt has the advantages of high strength, good elasticity, impact resistance, light weight and good groove performance. It can effectively reduce the transmission cost and realize high speed, large span and long distance transmission.
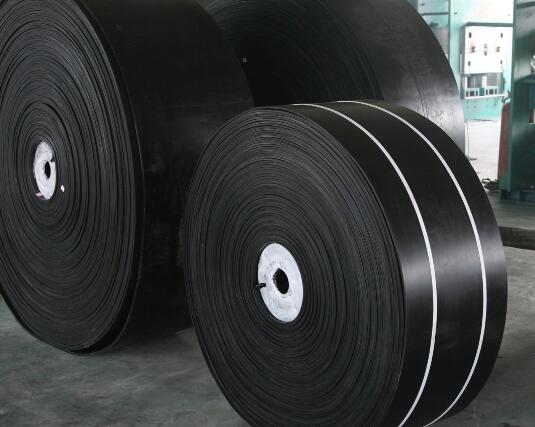
Nylon conveyor belt
Nylon core conveyor belt has the characteristics of thin body, high strength, impact resistance, good performance, high interlayer bonding strength, excellent flexure and long service life, suitable for medium and long distance, high load and high speed conditions of conveying materials. Nylon conveyor belt not only has these advantages, the most important thing is that it is fast and convenient, greatly improve the work efficiency and work integrity degree.
According to the different properties of covering glue, it is divided into cold resistance, acid resistance, alkali resistance, oil resistance, wear resistance and so on.
According to the different uses can be divided into lifting belt, power belt, conveyor belt.
According to the different structure can be divided into ordinary laminate type, plus transverse enhancement layer of impact resistance, tear prevention type.
(1) Material with core: NN 100, NN 150, NN 200, NN 300, NN 400, NN 500
(2) Bandwidth: 1,00 mm-3,000 mm
(3) cloth layer: 1-10 layer
(4) Coverage glue: working face: 1.5-8mm non-working face: 0mm-4.5mm
Interlayer bonding strength:
Indicator project | Between the cloth layer | Between the cover layer and the belt core | |
Overlay thickness of 0.8-1.5mm | Overlay thickness is> 1.5mm | – | |
Mean value of all samples, N/mm, not less than | 4.5 | 3.2 | 3.5 |
Minimum peak of all samples, N/mm is not less than | 3.9 | 2.4 | 2.9 |
Product characteristics
1,This product is refined from nylon canvas by calendering, molding, vulcanization and other processes.
2, the product to meet the requirements of different use conditions, can be made into different edge type, open edge type, ladder type, ladder type and other structures
Nylon conveyor belt is suitable for conveying non-corrosive bulk, granular, powder materials, such as coal, coke, sand, cement and other bulk materials (materials) or component articles, conveying various bulk, granular, powder and other loose materials with accumulation density of 6.5~2.5t/m3, can also be used for the transportation of adult articles.
characteristic:
1, with the body of good elasticity, impact resistance, wear resistance.
2, good flexure, easy to turn into the groove.
3,No mildew corrosion occurs.
technical norms:
National standard GB / T7984-2001
Nylon (NN) conveyor belt:
Overlayer: tensile strength not less than 15 Mpa, tear extension length not less than 350%, grinding consumption 200mm3
The average value of interlayer bonding strength of longitudinal samples is not less than 4.5 N/mm, and the average value between covering glue and cloth layer is not less than 3.2 N/mm
The elongation of full thickness longitudinal tear is not less than 10%, and the elongation of full thickness longitudinal reference force is not less than 4%.
Interbonding strength of nylon conveyor belt:
Indicator project | Between the cloth layer | Between the cover layer and the cloth layer | – |
The covering layer thickness is 1.5mm | Overlay thickness is> 1.5mm | – | |
The mean value of longitudinal samples is not less than | 4.50 | 3.2 | 3.50 |
The average value of transverse samples is not less than | 4.50 | 3.2 | 3.50 |
The highest peak of all samples is not greater than | 20 | 20 | 20 |
The minimum peak of all samples shall not be less than | 3.9 | 2.40 | 2.9 |
Conveyor belt joint method:
All the conveyor belts must be connected into a ring for use, so the quality of the conveyor belt joint directly affects the service life of the conveyor belt and whether the conveyor line runs smoothly. The common methods of conveyor joints include mechanical joints, cold bonding joints, hot vulcanized joints, etc.
Nylon conveyor belt maintenance and maintenance
- In the transportation and storage, the conveying tape should be kept clean to avoid direct sunlight or rain and snow, prevent contact with acid, alkali, oil, organic solvents and other substances, and be one meter away from the heating device.
- During storage, the warehouse temperature should be maintained between 18-40℃, and the relative humidity should be kept between 5080%.
- During the storage period, the product should be placed in volume without folding. During the storage period, the product should be turned once a quarter.
4, different types, specifications of the number of layer conveyor belt should not be used together, the best use of the joint bonding method.
- The type, structure, specification and layer number of the conveying tape should be reasonably selected according to the use conditions.
- The running speed of the conveying tape should generally not be greater than 2.5 m / s, and the materials with large mass and large wear and the unloading device using fixed pears should use low speed as far as possible.
- The relationship between the diameter of the transmission roller and the cloth layer of the conveyor belt, the supporting system of the transmission roller, the reversing roller and the requirements of the roller groove corner should be reasonably selected according to the design provisions of the conveyor.
- The feeding direction should follow the running direction of the tape, in order to reduce the impact of the tape when the material falls to reduce the falling distance of the material; The belt should shorten the roller distance and use the buffer roller for leakage, with a soft and moderate baffle board to avoid the material plate and scraping the surface of the conveyor belt.
- The following matters should be paid attention to in the use of the conveyor belt: ① Avoid the roller covered by material, resulting in poor rotation, prevent the roller and the tape, pay attention to the lubrication of the moving part, but not oil conveying tape; ② Avoid load start; ③ tape deviation, take measures to correct the application; ④ repair the local damage cotton application, so as to avoid expansion;
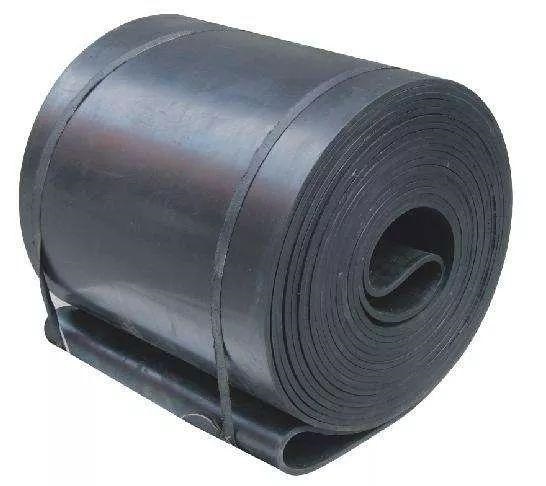
RUBBER CONVEYOR BELTS
The reason for the deviation
In the process of use, if there is a deviation, make the following check to determine the reason and adjust. The parts and treatment methods of the conveyor belt are:
(1) Check the non-coincidence degree between the transverse center line of the roller and the longitudinal center line of the belt conveyor. If the noncoincidence value exceeds 3mm, it shall be adjusted using the long mounting holes on both sides of the roller set. The specific method is which side of the conveyor belt, which side of the roller group to the direction of the conveyor belt, or the other side back.
(2) Check the deviation value of the two planes of the installed bearing seat of the head and tail frame. If the deviation of the two planes is greater than 1mm, the two planes shall be adjusted in the same plane. The adjustment method of the head drum is: if the conveyor belt deviates to the right side of the roller, the bearing seat on the right side of the roller should be moved forward or the left bearing seat backward; if the conveyor belt deviates to the left side of the roller, the left side of the roller should move forward or the right bearing seat backward. The tail drum is adjusted in the opposite way to the head drum.
(3) Check the location of the material on the conveyor belt. The material is not centered in the cross section of the conveyor belt, which will cause the conveyor belt to deviate.
If the material goes to the right, the belt deviates to the left and vice versa. When using, the material should be centered as far as possible. In order to reduce or avoid such conveyor belt deviation, it can increase the baffle plate and change the direction and position of the material.
There are many reasons for the deviation, which need to be treated according to different reasons.
- Adjust the bearing roller set
The belt of the belt conveyor can adjust the position of the roller set in the middle of the belt conveyor, and the mounting holes of the roller set are processed for adjustment. The specific method is which side of the belt, which side of the roller group forward direction of the belt, or the other side back. If the lower position of the roller group should be moved to the left, and the upper position of the roller group should be moved to the right.
- Install the centering roll set
There are many types of centering roll set, such as intermediate shaft type, four link type, vertical roll type, etc. The principle is to use the block or roll in the horizontal direction rotation block or produce transverse thrust to make the belt automatically centering to achieve the purpose of adjusting the belt deviation. Generally, this method is reasonable to use when the total length of the belt conveyor is short or the belt conveyor runs in both directions, the reason is that the shorter belt conveyor is easier to deviate and not easy to adjust. It is best not to use this method for the long belt conveyor, because the use of the centering roller set will have a certain impact on the service life of the belt.
- Adjust the position of the drive drum and the reversing roller
The adjustment of the drive drum and the direction change roller is an important part of the belt running deviation adjustment. Because a belt conveyor has at least 2 to 5 rollers, the installation position of all rollers must be perpendicular to the center line of the length direction of the belt conveyor, if the deviation is too large, the deviation will inevitably occur. The adjustment method is similar to the adjustment roller group. For the head roller such as the belt to the right side of the roller, the right bearing seat should move forward, the belt to the left side of the roller, the left bearing seat should move forward, the corresponding left bearing seat can also be moved back or the right bearing seat backward. The tail drum is adjusted in the opposite way to the head drum. After repeated adjustment until the belt to the ideal position. It is best to install the position accurately before adjusting the drive or reversing the roller.
- Adjustment of the tension point
The adjustment of belt tension is a very important part of the deviation adjustment of belt conveyor. In addition to the tension of the weight of the two sides of the roller should be perpendicular to the length of the belt direction should also be perpendicular to the gravity vertical line, that is, to ensure the level of the center line of its axis. When using screw tension or hydraulic cylinder tension, the two bearing holders of the tension drum should be translated to ensure that the shaft of the roller is perpendicular to the longitudinal direction of the belt. The specific adjustment method of the belt deviation is similar to that of the roller.
- The effect of the drop material position at the reprint point on the belt deviation
The drop position of the material at the transfer point has a great influence on the deviation of the belt, especially when the projection of the two belt conveyor is vertical. Usually, the relative height of the two belt conveyor should be considered. The lower the relative height, the greater the horizontal velocity component of the material, the greater the lateral impact on the lower belt, and the more difficult for the material to center. Deflate the material on the belt cross-section, eventually leading to the deviation of the belt. If the material goes to the right, the belt deviates to the left and vice versa. In the design process, the relative height of the two belt conveyor should be increased as much as possible. The form and size of the upper and lower funnel and guide groove of the moving bulk transport machinery should be considered more seriously considered. The width of the general guide groove should be about two-thirds of the width of the belt. In order to reduce or avoid the belt deviation, the baffle plate can be added to block the material, and change the falling direction and position of the material.
Six, the adjustment of the two-way running belt conveyor deviation
The adjustment of belt deviation of two-way operation is much more difficult than that of one-way belt conveyor. In the specific adjustment, we should first adjust one direction first, and then adjust another direction. When adjusting, carefully observe the relationship between the belt movement direction and the running trend, and adjust it one by one. The emphasis should be on the adjustment of the drive roller and the direction roller, followed by the adjustment of the roll and the adjustment of the material drop point. At the same time, it should be noted that the belt should be uniform in the direction of the length of the belt section, and the force on both sides should be as equal as possible when using the guide chain traction.
Debugging conveyor belt
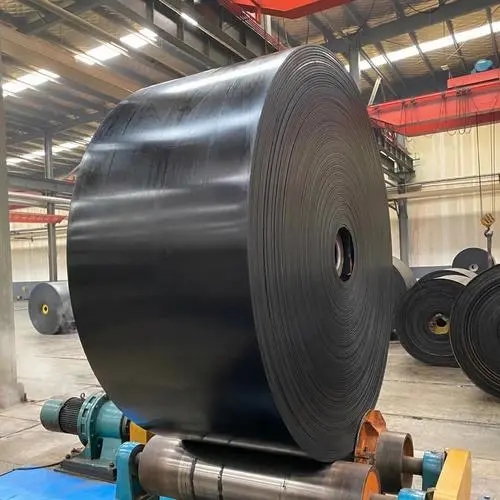
conveyor belt maintanced
The conveyor belt is the key equipment of the conveying system, and its safe and stable operation directly affects the production operation. The deviation of conveyor belt is the most common fault of belt conveyor, and its timely and accurate treatment is the guarantee of its safe and stable operation. There are many reasons for the phenomenon and cause of deviation, and different adjustment methods should be adopted according to different deviation phenomena and reasons to effectively solve the problem. This paper is based on years of field practice, from the user’s point of view, using mechanical principle to analyze and explain the causes of such faults.
- The axis of the head drive drum or the rear drum is not perpendicular to the center line of the conveyor, causing the conveyor belt in the deviation of the head drum or the tail to the roller. When the roller is deflection, the tightness of the conveyor belt on both sides of the drum is not consistent, and the traction force Fq along the width direction is not consistent, becoming an increasing or decreasing trend. In this way, the conveyor belt will add a decreasing moving force Fy, resulting in the deviation of the conveyor belt to the loose side, namely the so-called “loose but not tight”. The adjustment method is as follows: for the head roller such as the conveyor belt to the right side of the roller, the right bearing seat should be moved forward, the conveyor belt to the left side of the roller, the left bearing seat should be moved forward, the left bearing seat can also be moved backward or the right bearing seat backward. The tail drum is adjusted in the opposite way to the head drum. After repeated adjustment until the conveyor belt is adjusted to the more ideal position. It is best to install the position accurately before adjusting the drive or reversing the roller.
- The processing error of the outer surface of the drum, the uneven adhesive or wear will result in different diameter sizes, and the conveyor belt will deviate to the side with the larger diameter. The so-called “run big, not run small”. Force situation: the traction force Fq of the conveyor belt results in a moving force Fy to the large diameter side, and under the action of the force Fy, the conveyor belt is offset. For this case, the solution is to clean up the surface of the drum adhesive, processing error and uneven wear will be replaced down to re-process the glue treatment.
- The blanking position at the transfer point is not correct, which causes the deviation of the conveyor belt. The blanking position of the material at the transfer point has a great impact on the deviation of the conveyor belt, especially when the projection of the upper conveyor and the conveyor in the horizontal plane is vertical. Usually, the relative height of the two belt conveyor should be considered. The lower the relative height, the greater the horizontal velocity component of the material, the greater the lateral impact force of Fc on the lower belt, and the more difficult for the material to center. If the material on the cross section of the conveyor belt, the horizontal force of the impact force Fc eventually causes the belt to deviate. If the material goes to the right, the belt deviates to the left and vice versa.
For the deviation in this case, the relative height of the two conveyors should be increased as much as possible in the design process. The form and size of the upper and lower funnel, guide groove and other parts of the belt conveyor restricted by space should be taken more seriously. The width of the general guide groove should be about three-fifths of the width of the belt more appropriately. In order to reduce or avoid the belt deviation, the baffle plate can be added to block the material, and change the falling direction and position of the material.
- The perpendality error between the installation position of the bearing roller and the center line of the conveyor is large, resulting in the deviation of the conveyor belt in the bearing section. Belt forward to the roller a forward traction Fq, the traction force Fz and a transverse force Fc, the transverse force makes the roller axial movement, because the roller support is not axial movement, it will inevitably produce a reaction to the conveyor belt Fy, it makes the conveyor belt moving to the other side, leading to the deviation.
Knowing the force situation of the installation deviation of the bearing roller group, it is not difficult to understand the reason for the deviation of the conveyor belt, and the adjustment method will be clear.
The first method is to process the mounting holes on both sides of the roller group during the manufacture for adjustment. The specific adjustment method, the specific method is which side of the belt to bias, which side of the roller group toward the belt forward direction, or the other side to move back. If the lower position of the roller group should be moved to the left, and the upper position of the roller group should be moved to the right.
The second method is to install the roller set, roll set has a variety of types such as intermediate shaft type, four rod type, roller type, etc., its principle is to use block or roll in the horizontal direction rotation or transverse thrust makes the belt automatically centripetal for the purpose of adjusting belt deviation, the force situation and bearing roller group deflection force situation is the same. Generally, it is reasonable to use this method when the total length of the belt conveyor is short or when the belt conveyor runs in both directions, because the shorter belt conveyor is easier to deviate and not easy to adjust. It is better not to use this method, because the use of the centering roller set will have a certain impact on the service life of the conveyor belt.
maintenance method
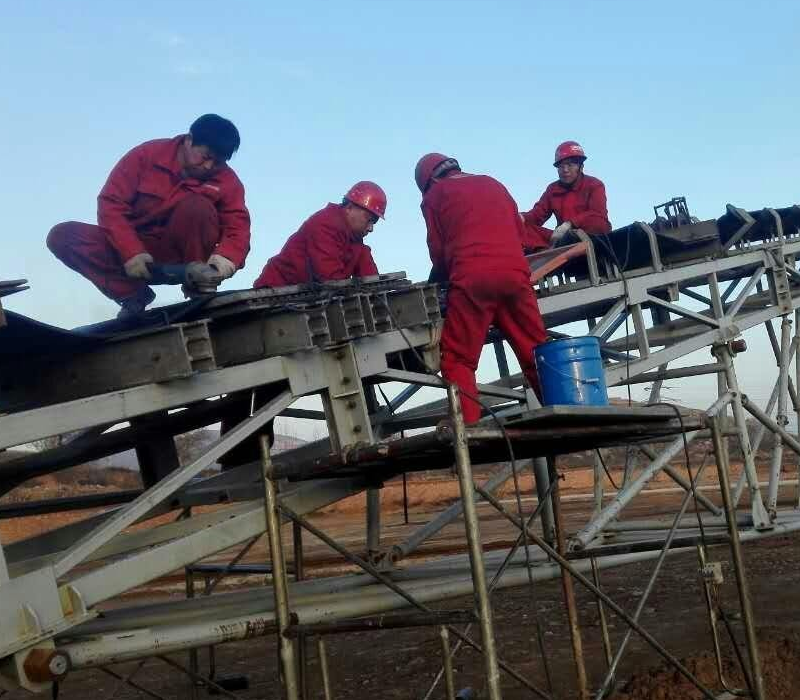
conveyor belts install
- In the transportation and storage, the conveyor belt should be kept clean to avoid direct sunlight, rain and snow immersion, to prevent contact with acid, alkali, oil, organic solvents and other substances affecting the quality of rubber, and 1 meter away from the heating device.
- During the storage time, the temperature in the warehouse should be kept between- -15℃ – – + 40℃, and the relative humidity should be kept between 50- -80%.
- The conveyor belt shall be placed in volume and not folded. It should be turned once a quarter during storage.
- The running speed of the conveyor belt should not be greater than 5.0 m / s, and the wear materials and the fixed plough unloading device should be used as far as possible. Excthe specified speed will affect the service life of the tape.
- The relationship between the diameter of the transmission drum of the conveyor and the cloth layer of the conveyor belt, the supporting of the transmission drum to the roller and the requirements of the roller groove corner should be reasonably selected according to the design provisions of the conveyor.
- In order to reduce the impact and wear of the material on the tape, the feed direction should be the running direction of the tape; the drop of the material to the tape should be minimized; the feed port should avoid the roller or roller; the tape section should shorten the roller spacing and take buffer measures. In order to prevent scraping the adhesive tape, the contact part of the retaining device and the tape should be the rubber plate with suitable hardness, rather than the tape head with the cloth layer.
- The following matters should be noted during the use of the conveyor belt:
- Avoid the roller being covered by the material, resulting in poor rotation, prevent the leakage from getting stuck between the drum and the tape, pay attention to the lubrication of the active part, but not the oil conveyor belt.
- Strive to avoid load startup.
- If the tape deviates, measures should be taken to correct it in time.
- Local damage of the tape should be repaired in time to avoid expansion.
- Avoid tape block from rack, pillar or block materials to prevent breaking and cracking.
Joint operation procedure
Nylon conveyor belt (cold vulcanized joint)
- Open the tape according to the actual size, add the joint length, recognize the top and bottom, and correctly delimit the end of the conveyor belt with the tape to connect the center line.(Check the center line) and draw the cut size line
- Preparation of the lower tape: the upper ends of the tape should be consistent with the running direction, and the marks of the upper tape and the lower tape should be marked.
(1) Draw a CB line with an Angle of 90 degrees at the end of the tape, and draw the oblique tangent according to the tape width of 0.3= about 16 degrees
(2) Draw a straight line parallel to the oblique tangent at the empty section (bottom side) 30mm away from the tape, keep the edge of the tape and mark it. Cut the marked 30mm wide tape strip into the slot and tear off the cover layer.
Nylon conveyor belt characteristics
Nylon conveyor belt is made of nylon canvas through calendering, molding, vulcanization and other processes. Compared with the ordinary cotton core conveyor belt, it has the advantages of high strength, good elasticity, impact resistance, light weight and good groove performance. It can effectively reduce the transportation cost to achieve high-speed, large-span, long-distance transmission.
1, with good elasticity, impact resistance, wear resistance.
2, good flexibility, easy to groove.
- No mildew corrosion occurs.
Nylon conveyor belt variety
According to the different properties of the covering glue, it is divided into cold resistant, acid and alkali resistant, oil resistant, wear resistant, heat resistant, flame retardant and so on.
According to the different uses can be divided into lifting belt, power belt, conveyor belt. According to the different structure can be divided into ordinary laminate type, plus transverse enhancement layer of impact resistance, tear prevention type
Determination requirements of wear resistance standards of nylon conveyor belt:
Reference to the international standard with rotating device to determine the wear resistance of conveyor belt rubber, the latest standard stipulates the sample in a certain level of sand cloth friction and wear, determine the volume of the conveyor belt wear consumption, to correct the sand cloth as the benchmark, the test results relative to some standard glue of volume wear consumption or wear index;
Under the specified contact pressure and a given area, lateral movement, wear is generated at the end of the cylindrical sample, measuring mass loss value to calculate the volume wear resistance, the material, wear consumption or wear index, the ratio of the wear consumption of standard nylon rubber transport belt and test rubber wear, in percentage.
Safety requirement
- Construction personnel must wear safety helmets when entering the construction site
- Operators must strictly abide by the coal mine safety operation rules
- It is strictly prohibited to work after drinking and to work illegally
- No hard bottom plastic shoes when entering the construction site
- Because the materials used for bonding are all flammable substances, they should be equipped with fire prevention equipment
- Choose the adhesive connection place, which should be in a place with good ventilation conditions
- The electrical equipment used shall be grounded
- The staff must concentrate and should not talk or laugh with others
- With glue connected in the environment with more dust, measures must be taken to build a shed
- Move the vulcanized appliances and pay attention to avoid injuries caused by scratches and collisions
- Wear a gas mask if the ventilation is bad or for a long time
- Smoking is strictly prohibited in the working area of the nylon conveyor belt
Leave a Reply
Want to join the discussion?Feel free to contribute!